Overview
The MAD 8X-10 M8SC10 Drone Arm Set is a propulsion system designed for industrial multirotor applications, including mapping, aerial inspection, firefighting, military operations, search and rescue, and defense. Equipped with the M8SC10 motor, 60A 14S FOC ESC, and Havoc polymer propellers, this system delivers up to 10.74kgf max thrust per rotor while maintaining high efficiency and reliability. The propulsion set is fully integrated and features neat cable arrangement, plug-and-play installation, and lightweight construction for optimized flight performance.
Key Features
- Provides 3.5-5kgf hovering thrust and up to 10.74kgf max thrust per rotor, supporting heavier payloads.
- Integrated propulsion system includes an M8SC10 brushless motor, 60A 14S FOC ESC, and Havoc 28x10 or 32x10.5 inch polymer propellers.
- Iron-core optimized motor delivers higher thrust with superior efficiency, using Japanese EZO bearings for durability.
- 60A FOC ESC features field-oriented control (FOC) algorithms for precise motor control, low-noise operation, and enhanced protection against over-voltage, over-current, and short circuits.
- Fully integrated arm set weighs 770g-803g, making it suitable for long-range flight applications.
- Available with SPRO AW 28x10-inch, HW 30x11-inch, or HAVOC 32x10.5-inch propellers, allowing users to optimize thrust and efficiency.
- Plug-and-play installation compatible with 30mm carbon tubes, offering quick setup with no complex wiring.
Technical Specifications
Parameter | 8X-10 |
---|---|
Max Thrust | 10.74kgf/rotor @48V |
Recommended Takeoff Weight | 3.5-5kg/rotor |
Voltage | 12S LiPo |
Operating Temperature | -20~60°C |
Combo Weight | 770-803g (depending on prop size) |
Compatible Carbon Tube | 30mm |
Propeller Sizes | 28x10", 30x11", 32x10.5" |
Propeller Weight | 170-202g/pc |
Motor Stator Size | 81x10 mm |
Motor Weight | 334g |
ESC Model | Circular 60A FOC |
Max Input Voltage | 60.9V |
Max Input Current | 60A |
Max Peak Current | 120A (10S) |
Max Throttle Signal Frequency | 50~450Hz |
ESC Compatibility | Ardupilot, DroneCan |
Applications
- Mapping and surveying
- Firefighting and emergency response
- Military and defense missions
- Industrial inspections
- Search and rescue operations
Details
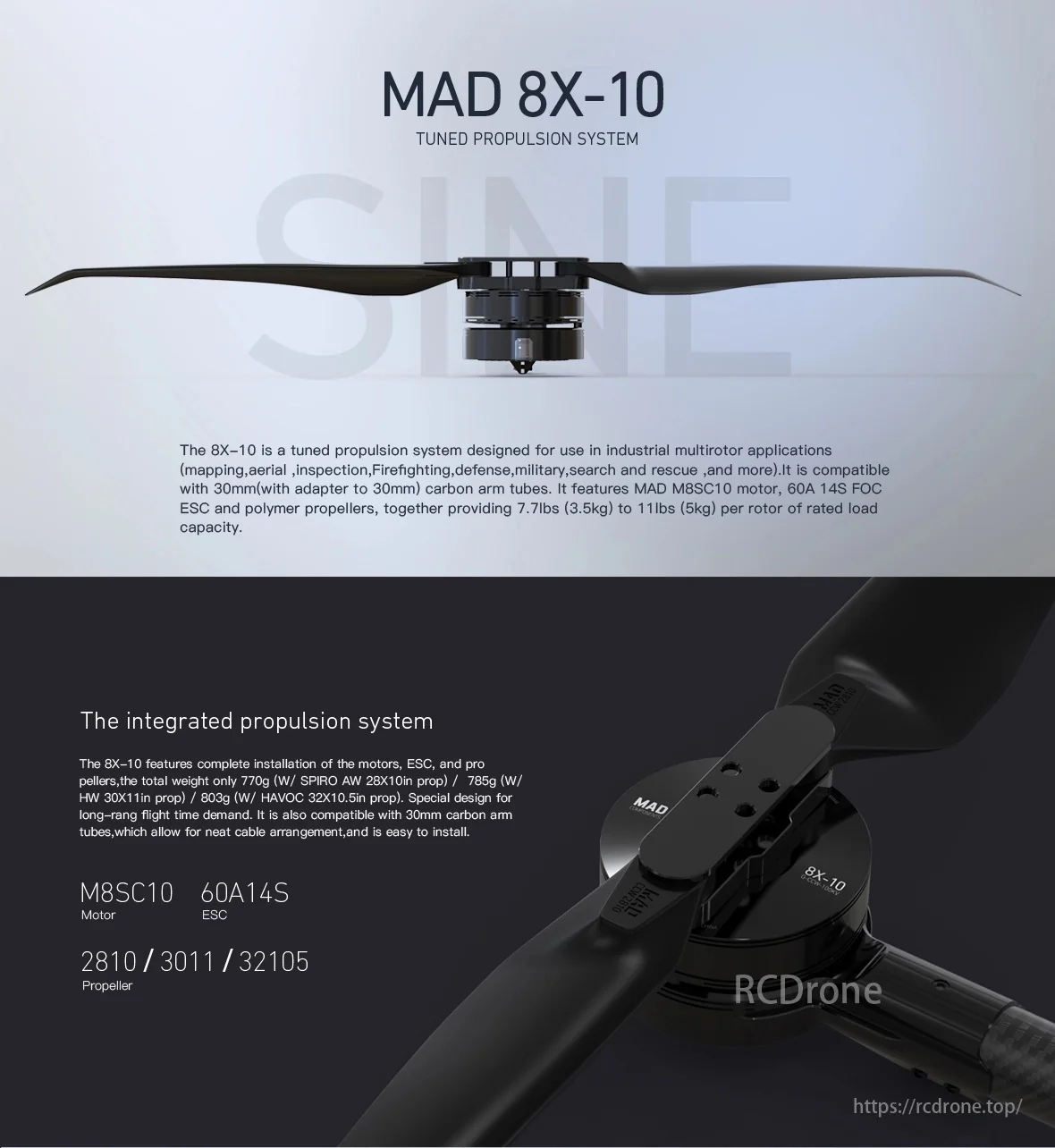
MAD 8X-10 is a tuned propulsion system for industrial multirotor applications. Compatible with 30mm carbon arm tubes, it features MAD M8SC10 motor, 60A 14S FOC ESC, and polymer propellers. Provides 7.7 to 11 lbs per rotor of rated load capacity. Total weight: 770g/785g/803g.

High efficiency motor uses new iron core design for bigger thrust and high efficiency. 3.5-5kgf per rotor, 10.7gf/w@4.7kg efficiency. Intelligent and reliable combo FOC60A14S ESC with FOC algorithms for responsiveness and precision control. Additional protection functions extend ESC life, ideal for harsh environments.
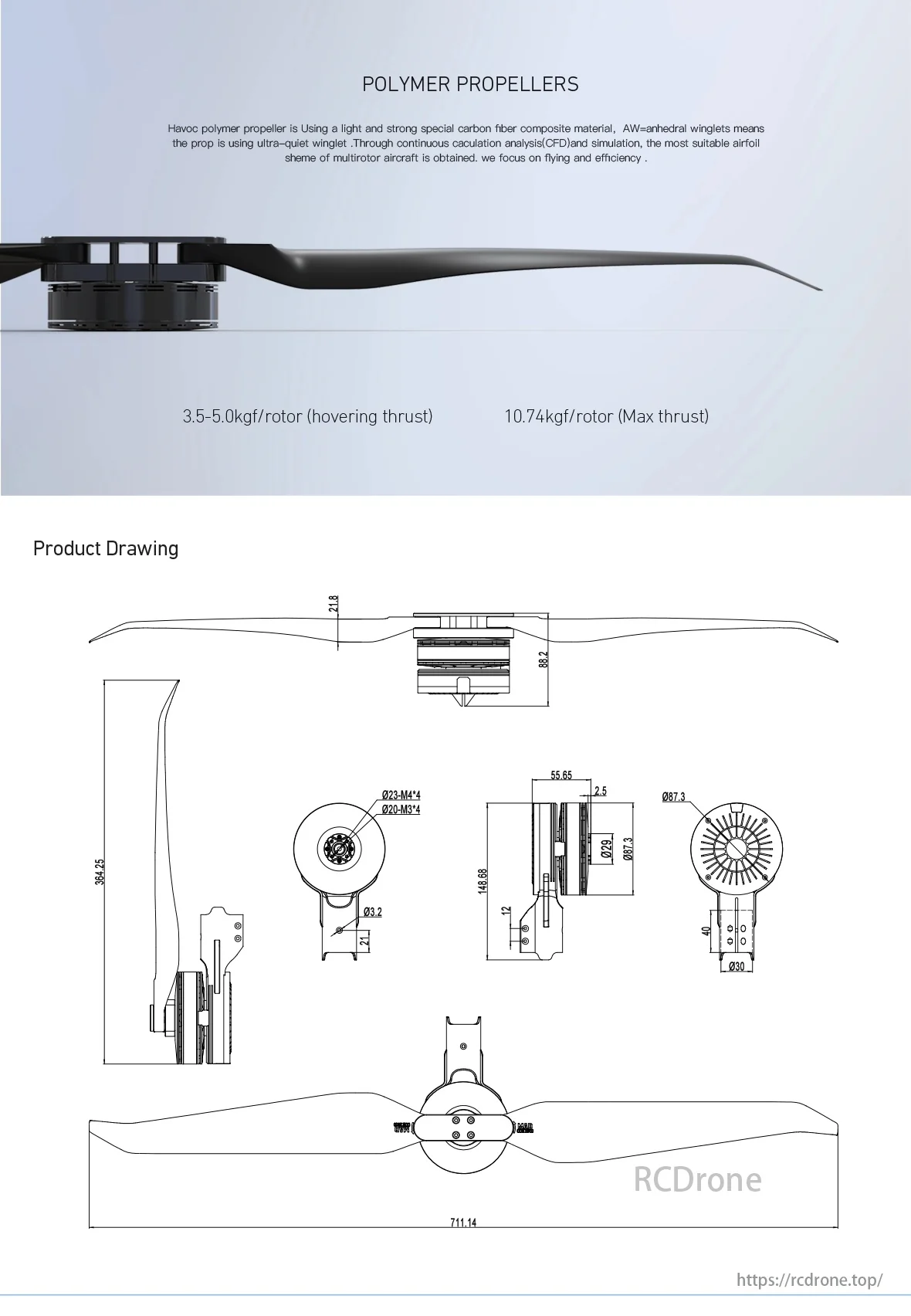
Polymer propellers use lightweight, strong carbon fiber composites. AW-anhedral winglets ensure ultra-quiet operation. CFD analysis optimizes airfoil shape for multicopter efficiency. Hovering thrust is 3.5-5.0 kgf/rotor, with a max thrust of 10.74 kgf/rotor. Detailed product drawings include dimensions and specifications.
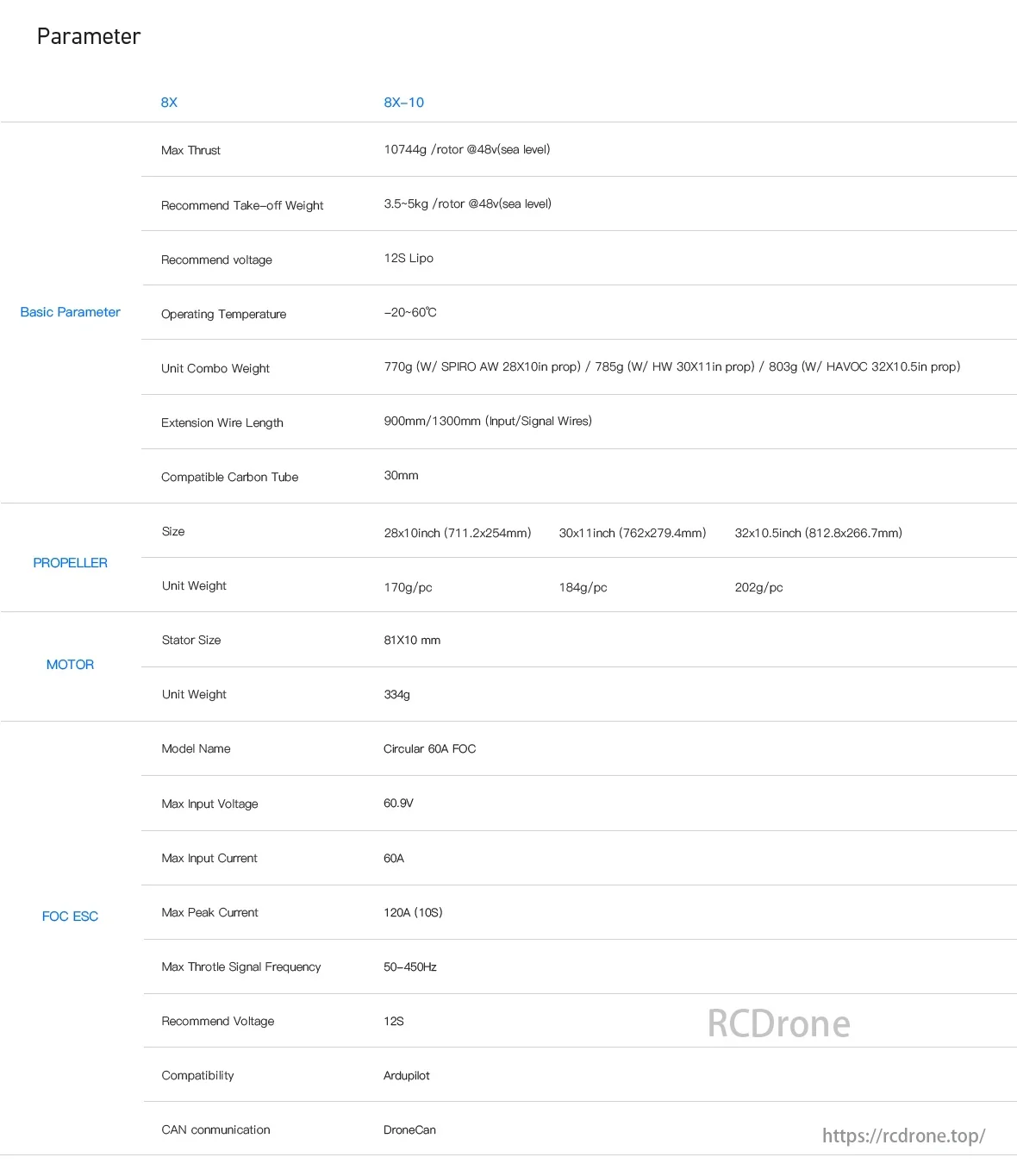
Specifications include max thrust of 10744g/rotor at 48V, recommended take-off weight of 3.5-5kg/rotor, operating temperature from -20 to 60°C, and compatible carbon tube length of 30mm. Propeller sizes vary, with weights ranging from 170g to 202g per piece. Motor has a stator size of 81x10 mm and weighs 334g. ESC supports up to 60A current.
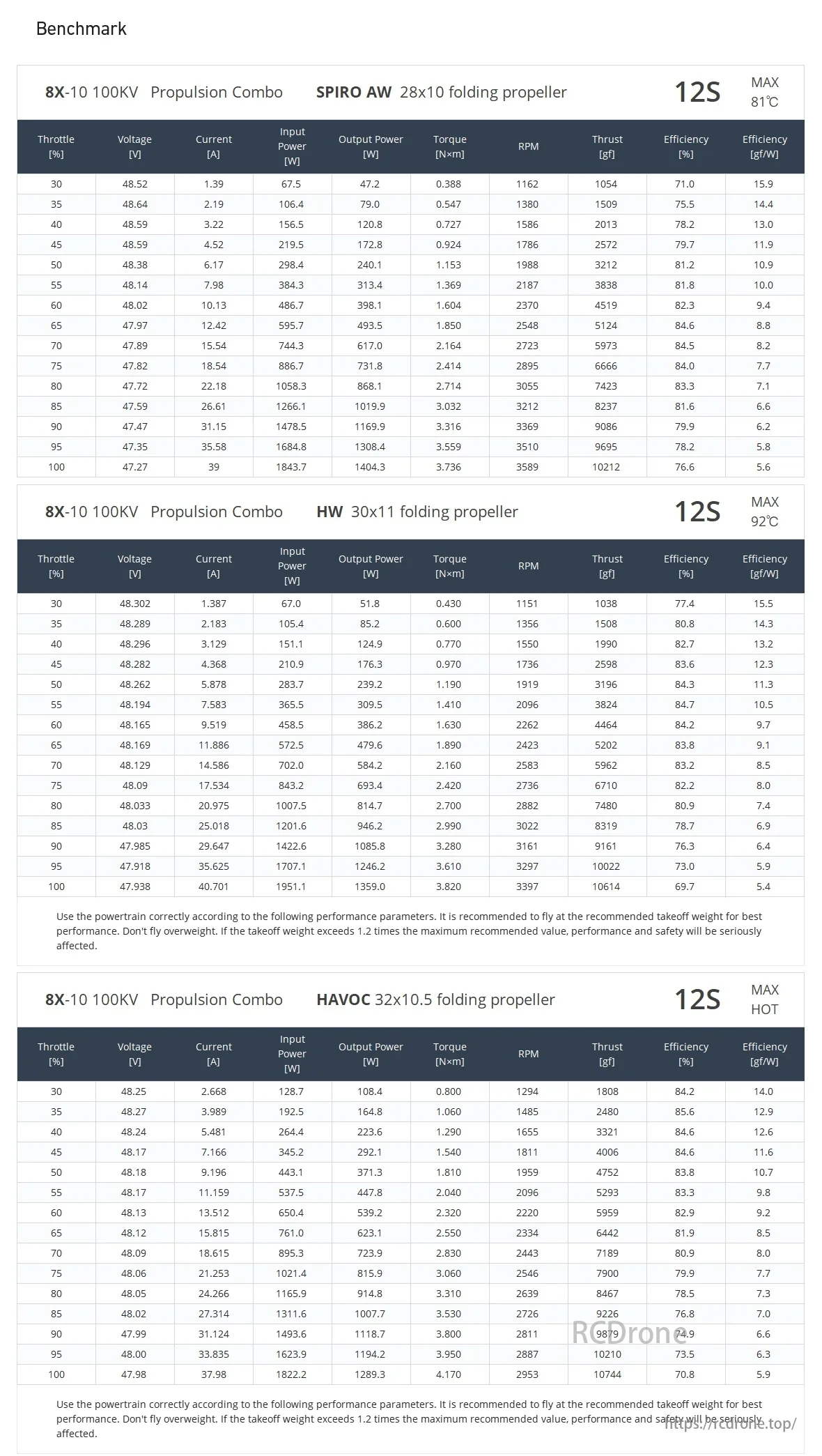
Benchmark data for 8X-10 100KV propulsion combo with three propellers: SPIRO AW, HW, and HAVOC. Tables detail throttle, voltage, current, power, torque, RPM, thrust, efficiency, and max temperature across various settings. Optimal performance advised at recommended takeoff weight; overloading impacts safety and performance.
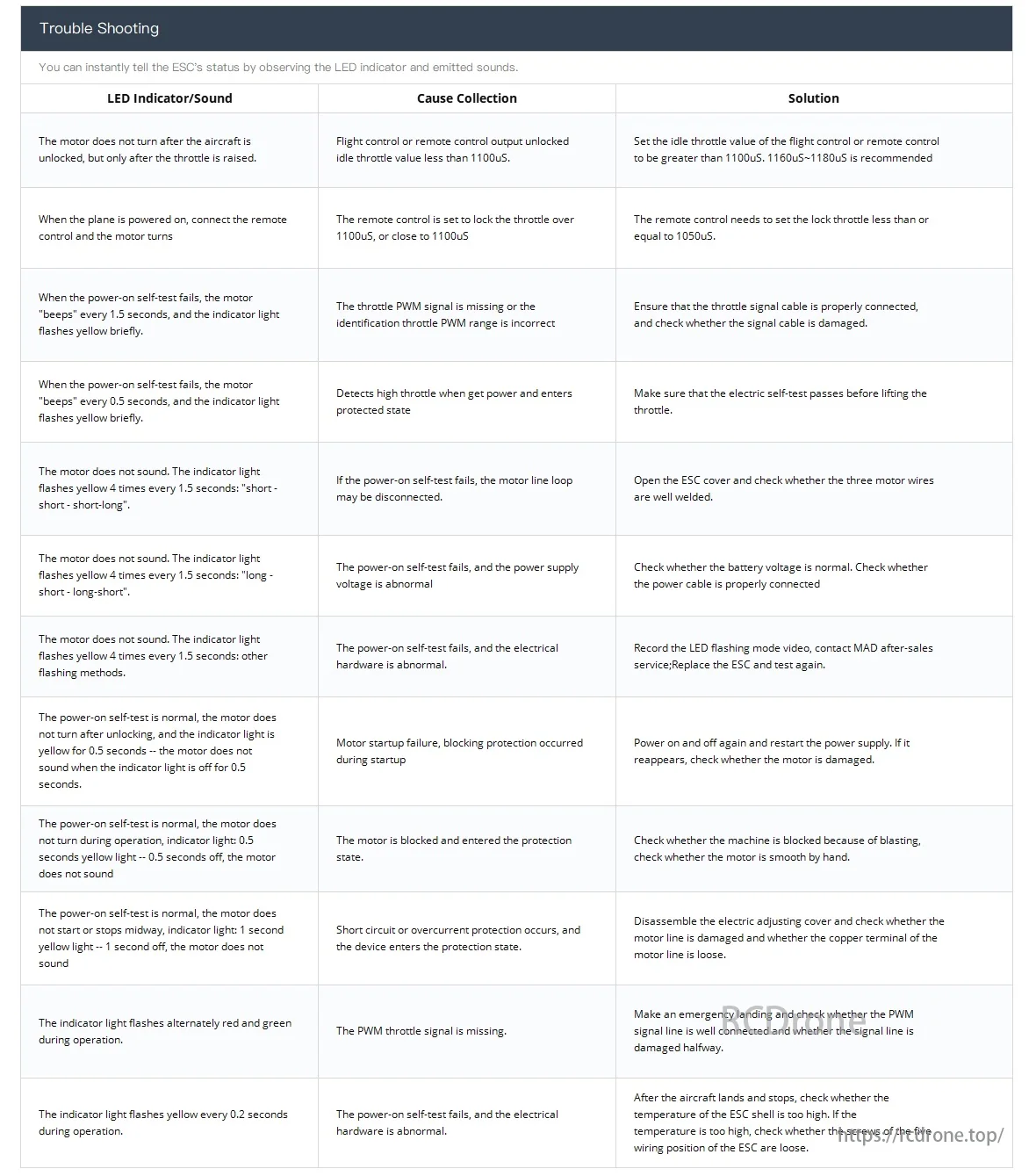
Troubleshooting guide for ESC issues. LED indicators and sounds diagnose problems like motor not starting, incorrect throttle settings, or hardware faults. Solutions include adjusting idle values, checking connections, ensuring proper self-test completion, and verifying power supply and wiring integrity.
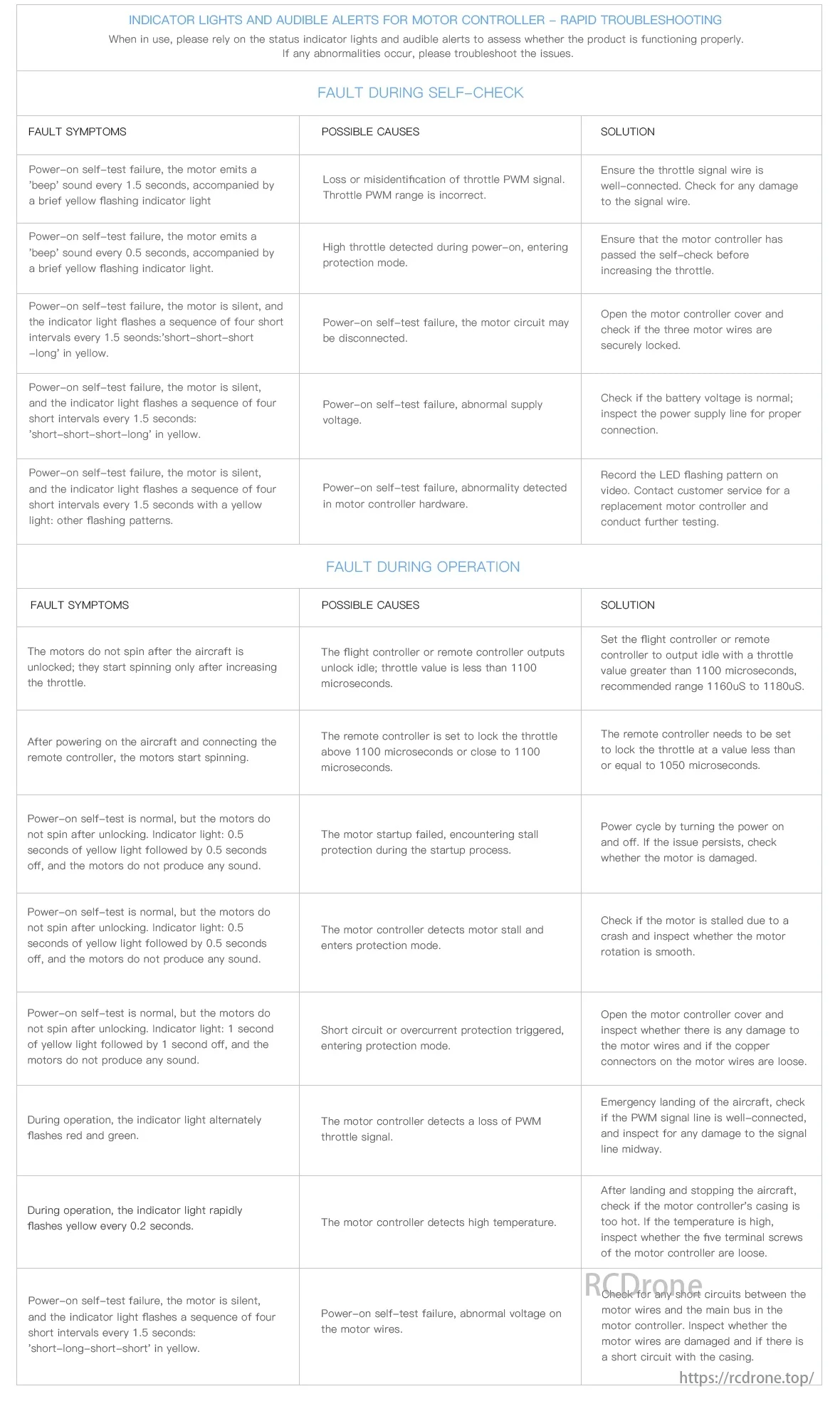
Indicator lights and audible alerts for motor controller troubleshooting. Faults during self-check include beeps, flashing lights, and silent motors due to signal issues or hardware abnormalities. Solutions involve checking connections, voltage, and motor wiring. Operation faults address spinning delays, remote settings, and temperature checks.