Overview
The MAD FOC IGBT 60A (80–440V) Drone ESC is a high-voltage, high-reliability electronic speed controller designed for large UAVs, industrial drones, and other demanding applications that require stable, efficient power at voltages up to 440 V. Built around advanced IGBT technology and featuring a field-oriented control (FOC) algorithm, this ESC ensures precise speed regulation, strong low-speed torque, and excellent overall efficiency in both sensorless and sensor-based motor setups.
Key Features
-
Wide Voltage Range (80–440 V)
Accepts up to 100S LiPo battery packs (or equivalent DC sources), delivering ample power for large-scale drones, heavy-lift systems, and industrial equipment. -
60A Continuous Current
Provides reliable performance for motors requiring sustained high current, enabling up to 60A of continuous output under proper cooling conditions. -
IGBT-Based Full-Bridge Inverter
Utilizes robust IGBT transistors for high-voltage operation, reduced conduction losses, and better thermal management compared to conventional MOSFET solutions. -
Advanced FOC Algorithm
Sensorless or sensor-based field-oriented control maintains stable torque at low speeds, smooth acceleration, and high power efficiency under varying load conditions. -
Multiple Protection Mechanisms
Includes under-voltage, over-voltage, over-current, and over-temperature protection. When triggered, the ESC either stops or limits output to safeguard both the motor and power system. -
IP-Grade Aluminum Heatsink
The heavy-duty heatsink design and aluminum enclosure provide excellent heat dissipation, ensuring continuous performance under demanding loads. -
Flexible Control Signal Standard
Default control follows standard RC PWM (50 Hz with 1150–1950 μs pulse width, up to 400 Hz max). An optocoupler isolates the control signal from the high-power stage for enhanced safety and noise immunity.
Technical Specifications
Item | Details |
---|---|
Model | MAD FOC IGBT 60A (80–440V) ESC |
Input Voltage Range | 80–440 V (up to 100S LiPo) |
Continuous Current | 60 A |
Instant/Peak Current | 60 A (dependent on thermal conditions) |
Control Method | Field-Oriented Control (FOC), sensorless or sensored |
Protection Features | Under-voltage, over-voltage, over-current, over-temp |
Control Signal | Standard PWM (50–400 Hz); optically isolated |
Dimensions (Approx.) | Refer to drawing (e.g., ~190×84×45 mm) |
Cooling | Convection cooling via aluminum heatsink |
Recommended Motors/Props | Examples: M15 KV13 or M36C10 KV10 at 400 V with S6254 prop |
Protection Mechanisms
-
Under-Voltage Protection
If the input voltage drops below the set threshold, the ESC stops output to protect the power system. -
Over-Voltage Protection
If the input voltage exceeds the specified upper limit, the ESC halts output, preventing damage from excessive voltage. -
Over-Current Protection
If motor current goes beyond the configured maximum, the ESC will either limit or cease output to safeguard both motor and ESC. -
Over-Temperature Protection
If internal temperature rises above safe levels, the ESC reduces or stops power to prevent thermal damage.
Control Logic
-
Standard RC PWM
By default, the ESC is controlled via a 50 Hz PWM signal with a pulse width range of 1150–1950 μs. -
Up to 400 Hz
For applications requiring faster response, the ESC can handle higher PWM frequencies (up to 400 Hz). -
Optical Isolation
The control signal is electrically isolated from the power stage for improved noise immunity and operational safety.
Installation & Wiring
-
Power Cables
- Positive (+): Connect the high-voltage DC input (up to 440 V).
- Negative (–): Connect the return path for the power supply.
-
Motor Cables
- Three-phase output cables to the motor. Ensure correct phase wiring if using hall sensors or other feedback.
-
Signal/Control Cable
- Typically includes a ground wire (signal ground) and a PWM input wire.
- Some configurations may include additional wires for CAN/RS232/RS485 communication or sensor inputs (depending on model variants).
-
Mounting & Cooling
- Attach the ESC securely using the provided mounting holes.
- Ensure adequate airflow around the heatsink for optimal cooling. Forced-air or liquid cooling may be considered in extremely high-load scenarios.
Troubleshooting
-
Motor Does Not Start
- Check that input voltage is within 80–440 V.
- Verify throttle signal and confirm ESC wiring.
-
Motor Stuttering or Vibration
- Re-check motor phases and any sensor connections (if used).
- Ensure ESC parameters match the motor specifications.
-
Excessive Heat or Shutdown
- Improve cooling or reduce load.
- Confirm motor and propeller are suitable for the application.
-
Voltage Out of Range
- If voltage exceeds 440 V or drops below 80 V, the ESC protection will engage. Adjust battery configuration accordingly.
Disclaimer & Safety
-
High-Voltage Precautions
Operating up to 440 V DC requires strict adherence to safety protocols. Only qualified personnel should handle installation and maintenance. -
Local Regulations
Comply with all regional laws and regulations governing UAVs, industrial robotics, or other high-power systems. -
Modifications & Liability
Unauthorized modifications, or using third-party components not specified by the manufacturer, may lead to unpredictable risks. Users assume responsibility for any resulting damage or injury. -
Maintenance
Regularly inspect connections, cables, and mounting hardware to ensure ongoing safety and performance.

AMPX 60A ESC features premium materials, rugged design, and good heat dissipation. It uses IGBT three-phase full bridge inverter topology with a peak output current of 200A. Sensor-less FOC technology ensures efficient, safe driving. Specifications include DC80V-440V input, ≤DC60A input current, ≤AC120A output current, and ≥98% working efficiency.

ESC protection mechanisms include undervoltage, overvoltage, throttle detection, sensor zero-point, and overtemperature protection. Communication protocol is IG-UART_V1.2 with a 19200 baud rate. ESCs are compatible with most DC brushless motors. Throttle calibration involves connecting PWM to the receiver, setting max and min throttle positions, and saving settings.
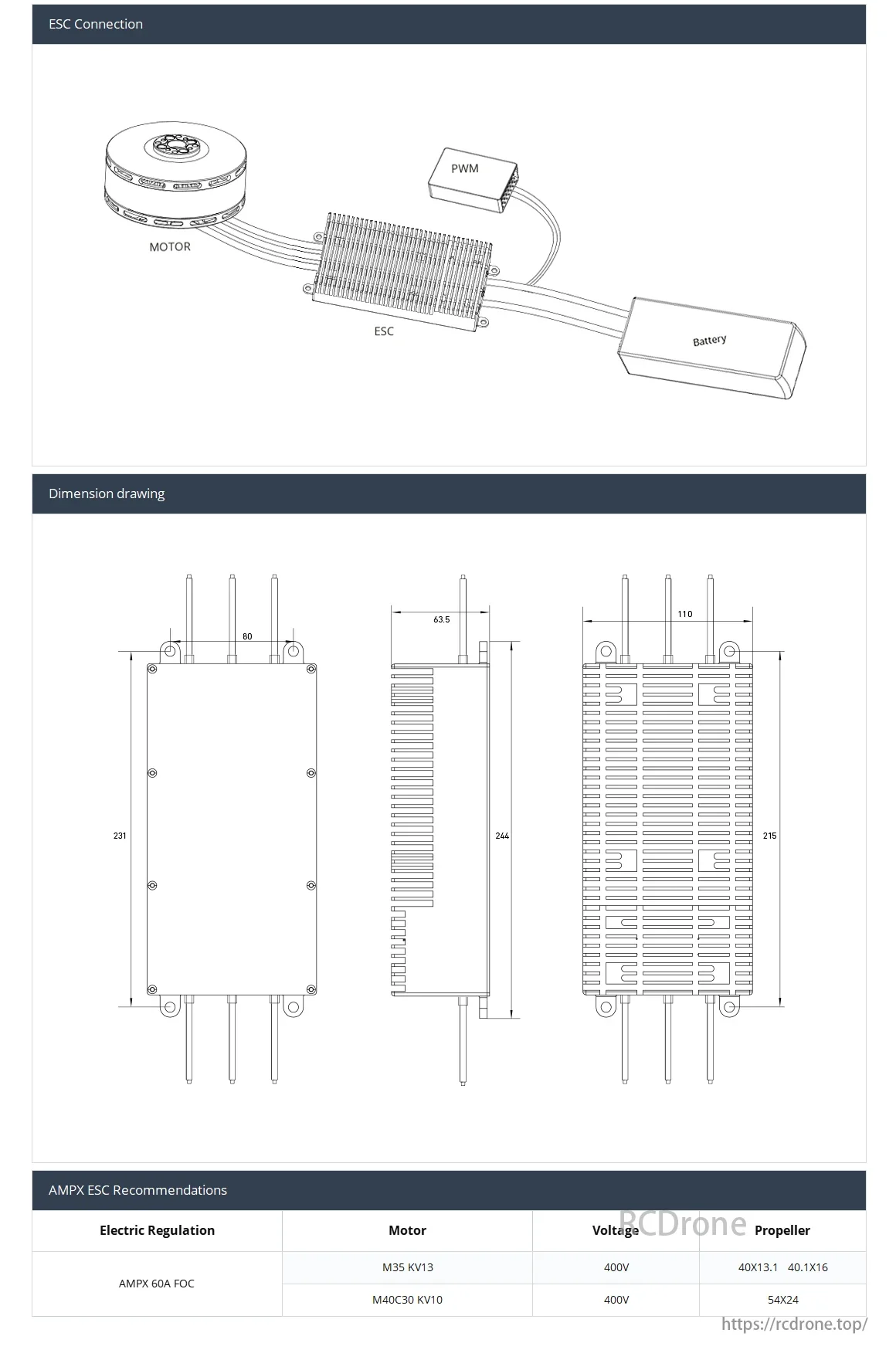
ESC Connection diagram illustrates motor, PWM, ESC, and battery setup. Dimension drawing provides measurements. AMPX 60A FOC recommends M35 KV13 or M40C30 KV10 motors with specific propellers.